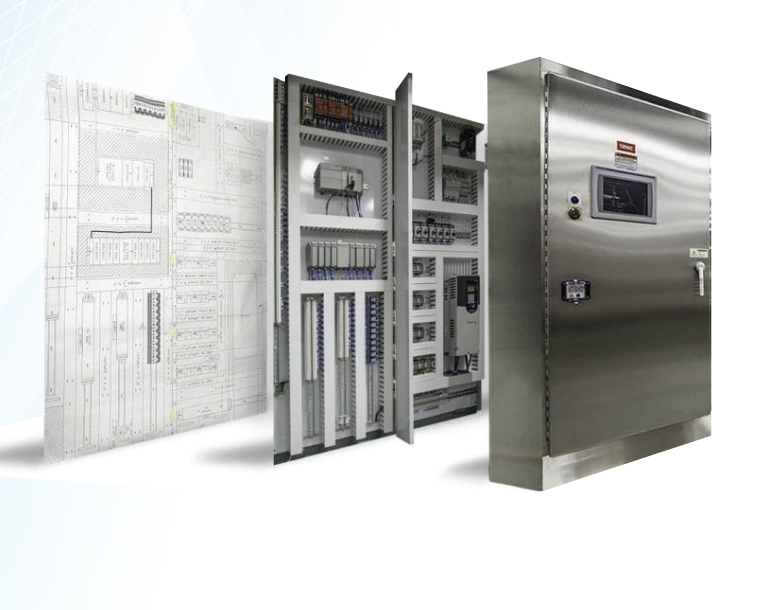
Before starting any electrical control panel project, we need to have a clear idea understanding of the manufacturing process requirements and safety standards. This knowledge enables us to design a set of electrical schematics and panel layouts that include all the necessary details such as power requirements, equipment specifications, signal types, and safety features. The design should be customized to our manufacturing process needs. The design should be reviewed by our technical team to ensure functionality, rating and safety requirements will be met. During the design review, it’s crucial to ensure that the control panel complies with all applicable Electrical Safety Standards, IEC 61439 and IEC 61439-2
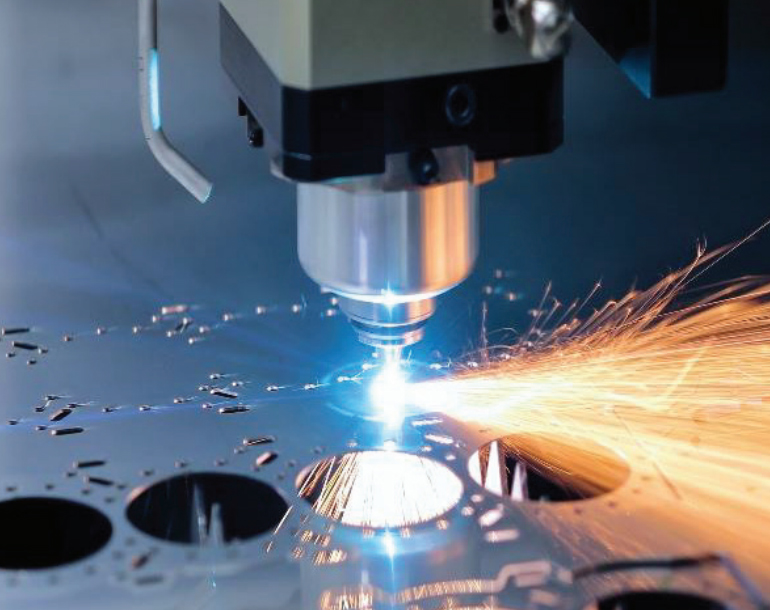
The sheet metal fabrication is the process of forming metals sheets to the desired shape using different manufacturing methods. The completion of a product usually comprises of many steps from cutting of the sheets, CNC punching, bending of the sheet and finally welding to the finished fabricated panel.
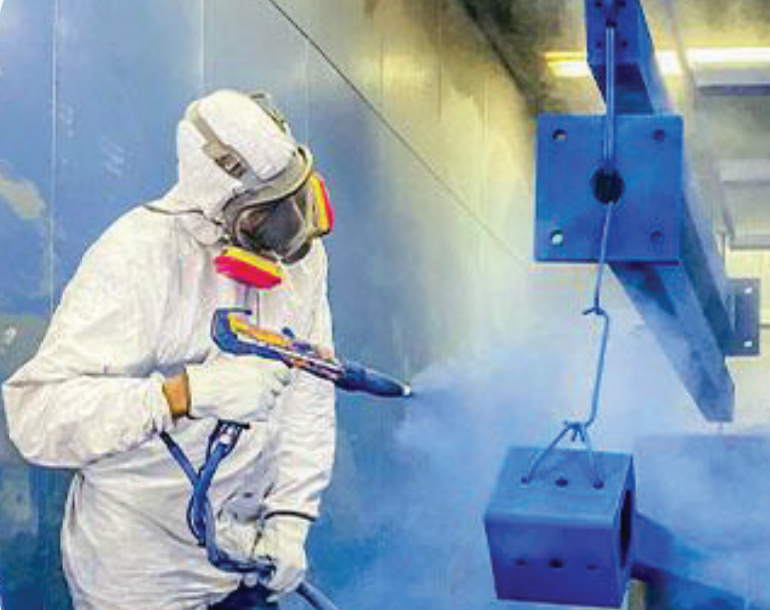
When we produce distribution boards, metal enclosure and electrical cabinets in order to anti resting and corrosion, we will clean the steel surface and level the material by using putty and coating by textured polyester powder with the oven by heating up to 200°C. usually our product maintains a powder coated thickness of 80-120μ.
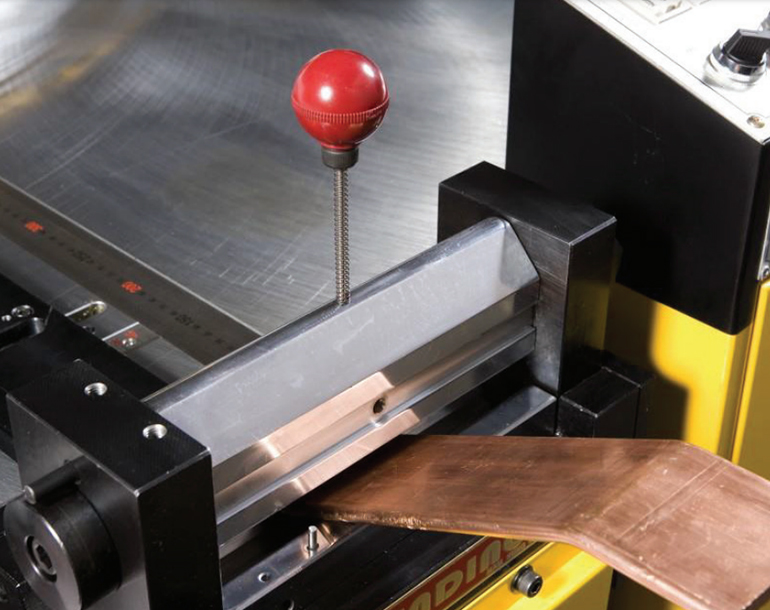
Busbar is the major part in an electrical panel system and plays a vital role for the efficient distribution and management of electrical power. The busbar is a conductor or group of conductors are responsible for distributing electrical power from a transformer or generator to various loads. Copper and Aluminum are the most common materials used for the busbar. Copper has high conductivity and melting point, which makes it an ideal choice for the busbar as well as suitable for high voltage applications. The process involves in the busbar fabrication are cutting, punching and bending.
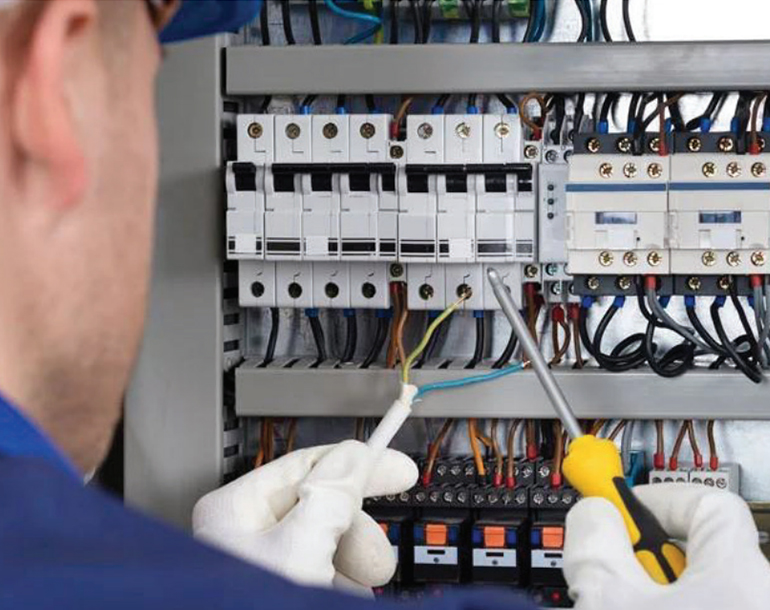
AAMI Technology panel assembly and wiring build electrical panel boards to meet our client specification technically and also follows IEC 61439-1&2.
Being a panel builder in the Kingdom, panel assembly and wiring service provider, we are committed to customer service, quality assurance and on time delivery.
AAMI always keeps efficient space for the component’s arrangements and effective cable terminations.
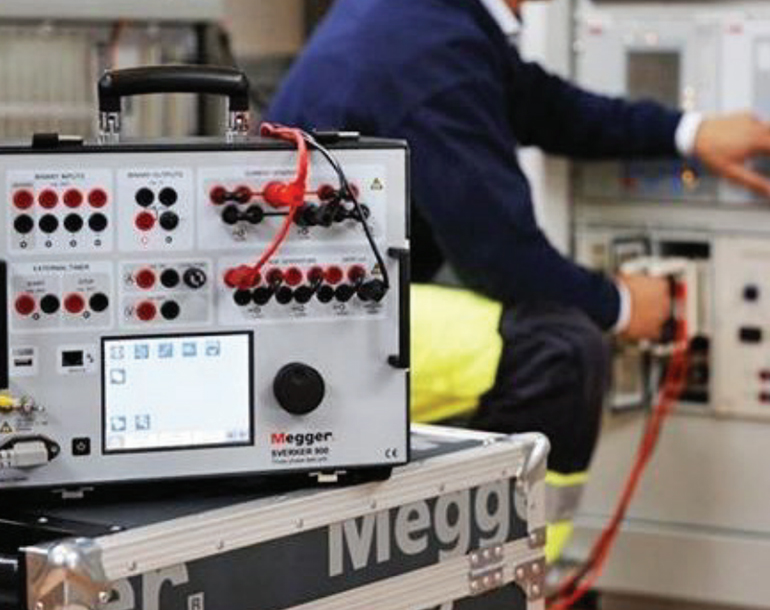
Quality assurance on electrical panels involves thorough inspection and testing to ensure compliance with specifications, safety standards, and functionality (operation sequence). This includes checking components, wiring, and connections for proper installation, as well as conducting performance tests to verify the panel’s reliability and efficiency. Regular maintenance and adherence to industry regulations are essential for optimal performance and safety.
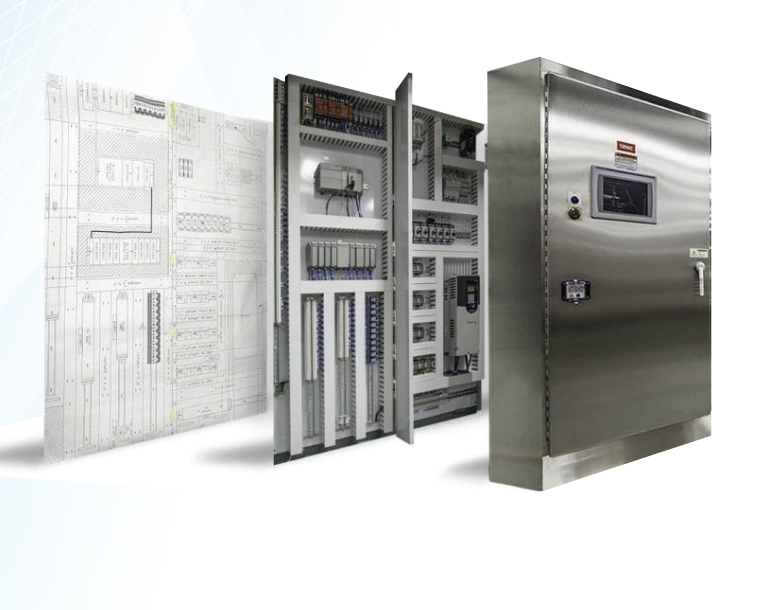
Before starting any electrical control panel project, we need to have a clear idea understanding of the manufacturing process requirements and safety standards. This knowledge enables us to design a set of electrical schematics and panel layouts that include all the necessary details such as power requirements, equipment specifications, signal types, and safety features. The design should be customized to our manufacturing process needs. The design should be reviewed by our technical team to ensure functionality, rating and safety requirements will be met. During the design review, it’s crucial to ensure that the control panel complies with all applicable Electrical Safety Standards, IEC 61439 and IEC 61439-2
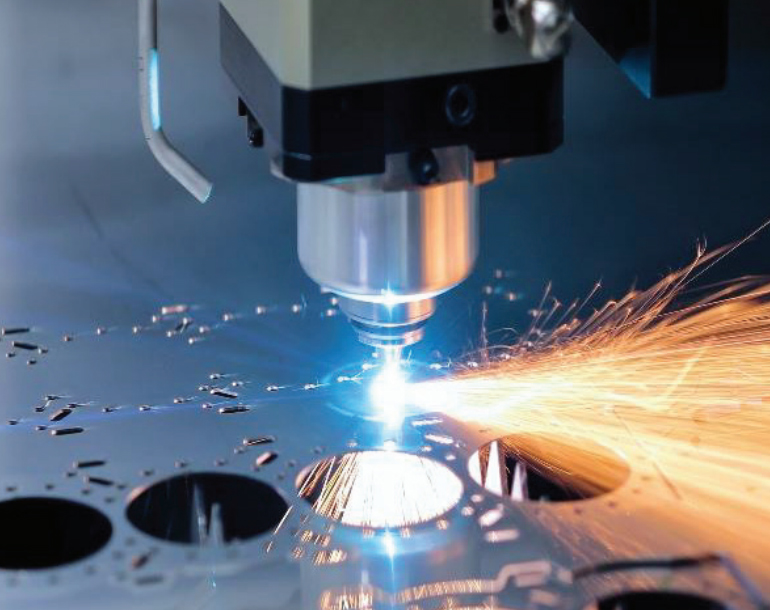
The sheet metal fabrication is the process of forming metals sheets to the desired shape using different manufacturing methods. The completion of a product usually comprises of many steps from cutting of the sheets, CNC punching, bending of the sheet and finally welding to the finished fabricated panel.
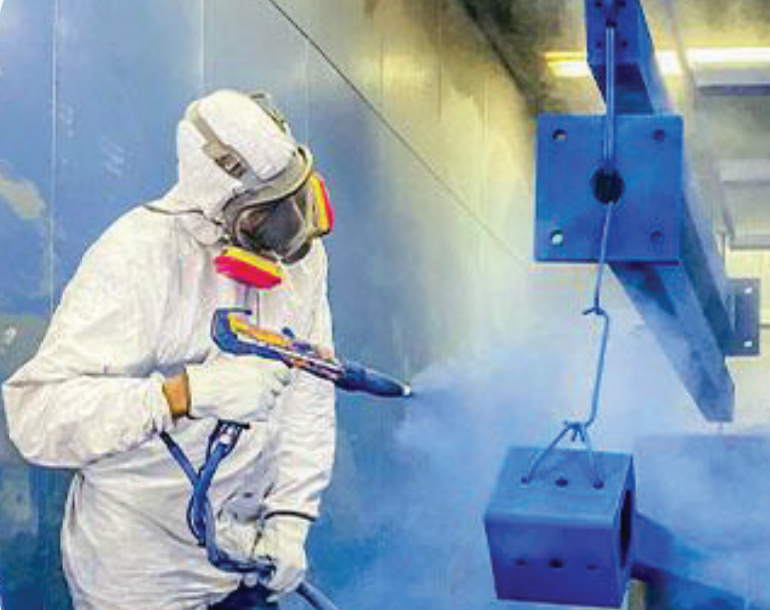
When we produce distribution boards, metal enclosure and electrical cabinets in order to anti resting and corrosion, we will clean the steel surface and level the material by using putty and coating by textured polyester powder with the oven by heating up to 200°C. usually our product maintains a powder coated thickness of 80-120μ.
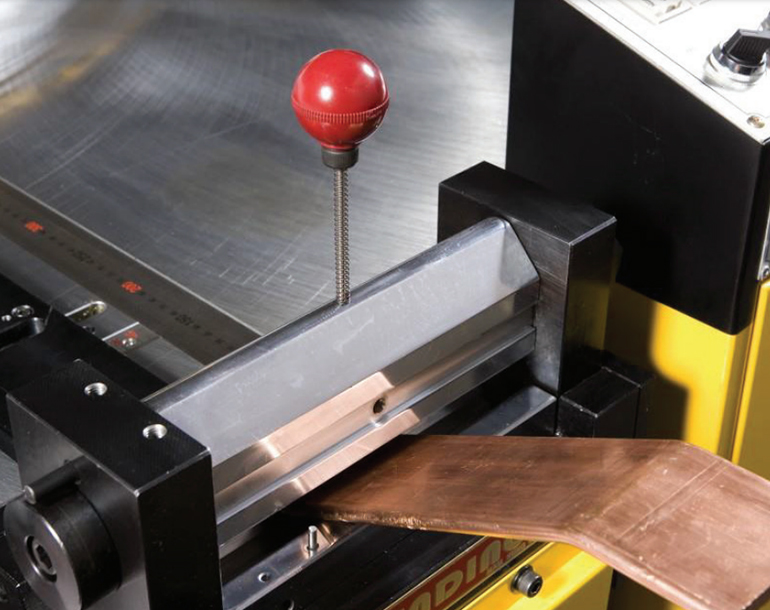
Busbar is the major part in an electrical panel system and plays a vital role for the efficient distribution and management of electrical power. The busbar is a conductor or group of conductors are responsible for distributing electrical power from a transformer or generator to various loads. Copper and Aluminum are the most common materials used for the busbar. Copper has high conductivity and melting point, which makes it an ideal choice for the busbar as well as suitable for high voltage applications. The process involves in the busbar fabrication are cutting, punching and bending.
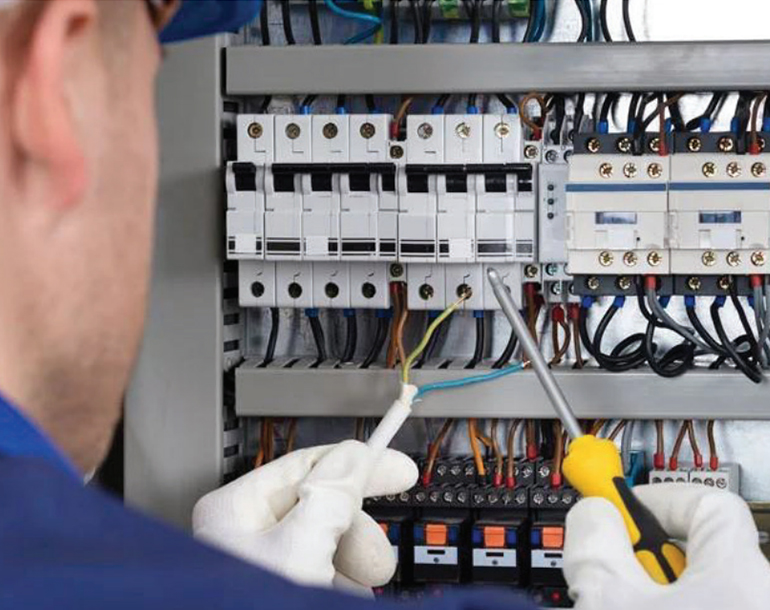
AAMI Technology panel assembly and wiring build electrical panel boards to meet our client specification technically and also follows IEC 61439-1&2.
Being a panel builder in the Kingdom, panel assembly and wiring service provider, we are committed to customer service, quality assurance and on time delivery.
AAMI always keeps efficient space for the component’s arrangements and effective cable terminations.
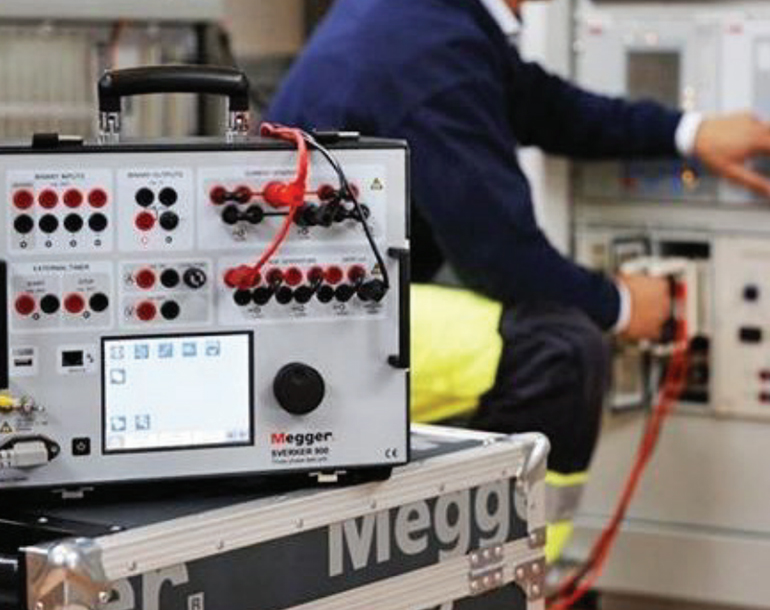
Quality assurance on electrical panels involves thorough inspection and testing to ensure compliance with specifications, safety standards, and functionality (operation sequence). This includes checking components, wiring, and connections for proper installation, as well as conducting performance tests to verify the panel’s reliability and efficiency. Regular maintenance and adherence to industry regulations are essential for optimal performance and safety.